The Alpha Process
THE ALPHA PROCESS: FASTER, MORE EFFICIENT SHELL SAND CASTINGS. TRANSLATION: PREMIUM CASTINGS WITHOUT A PREMIUM PRICE.
THE ALPHA PROCESS
The Alpha Process fills a void among other molding processes with a variation of the Shell Sand Process (which is widely used in foundry core production, though relatively rare for molding). It uses a special resin-coated sand that fuses together when baked in a heated core or mold pattern.
The resulting core/mold produces exceptional sand-cast surface finish, dimensional stability, and more delicate casting features compared to other sand processes due to the toughness of the cured core/mold.
Unfortunately, this fine grain shell sand is expensive, takes time to cure, and when used traditionally, proves difficult to remove from the poured casting, making shell sand molding expensive and slow.
Developed and patented by second-generation owner Robert Barron and fully implemented by his son Emerson Barron, the Alpha Process takes advantage of shell molding’s best qualities by producing a relatively thin shell at the casting surface and backfilling the mold with coarser, faster-curing, and reusable sand.
This uses less shell sand to create a core and mold set that’s less expensive, faster to produce, easier to remove, and provides better venting to minimize porosity defects in the casting.
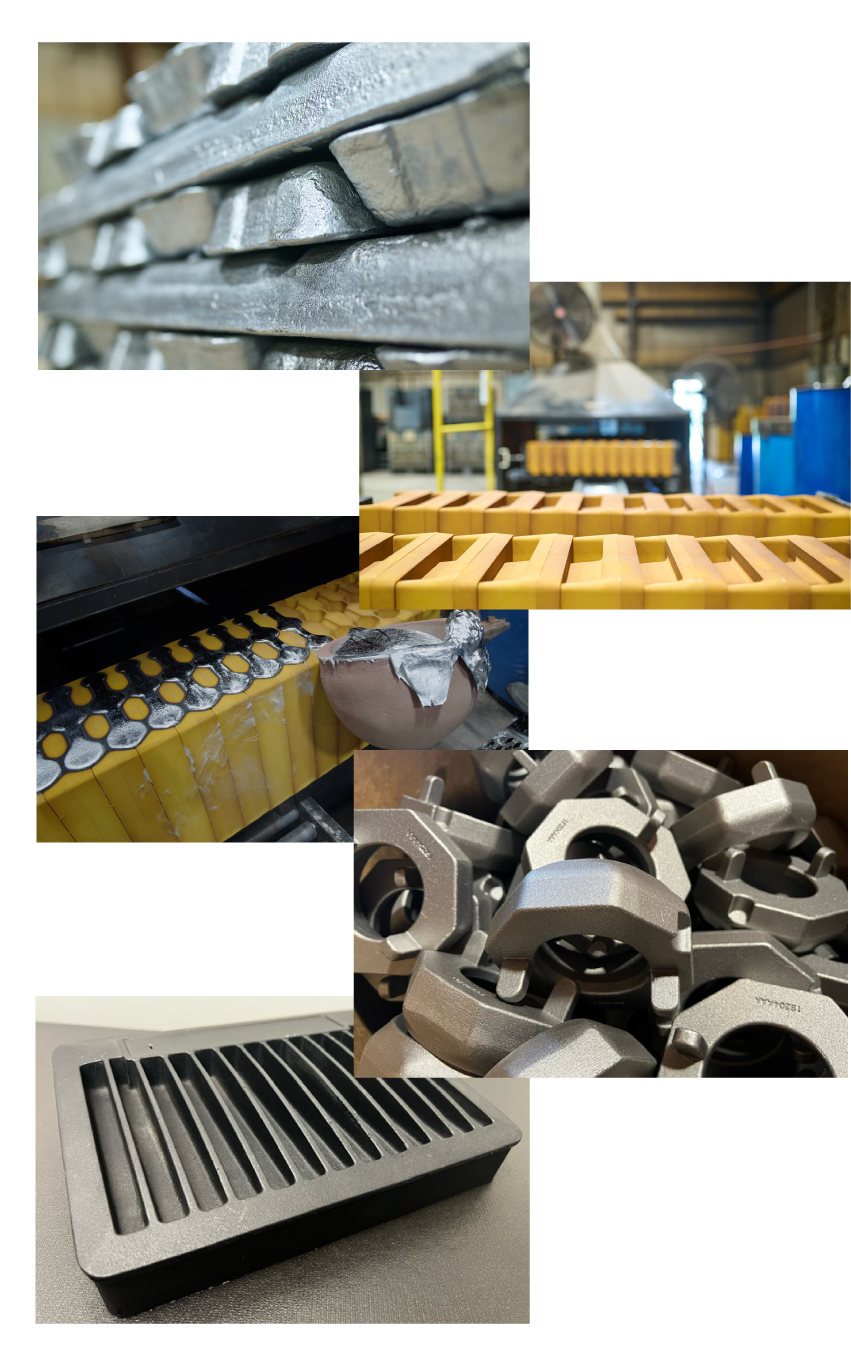
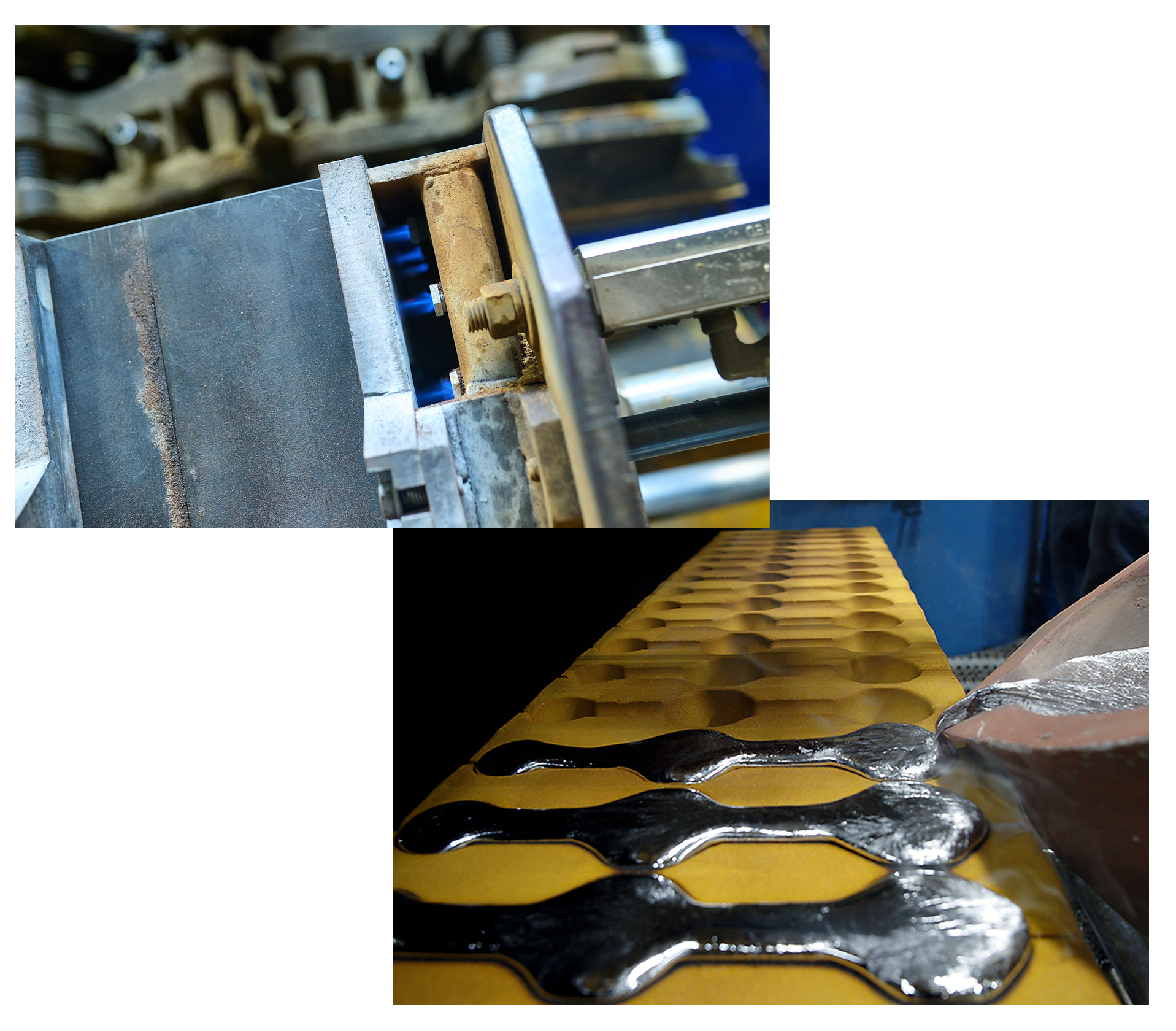