Our Equipment
NEW! ALPHA FOUNDRY WELCOMES THE EXONE™ S-MAX®
This changes everything! The S-Max® increases our capacity, enhances our production, and can offer our customers more value. The S-Max® is the smartest, most advanced 3D sand printer and it’s now available from Alpha Foundry. With this new equipment we can provide:
• Lights-out manufacturing with less hard-to-find labor
• Design freedom to consolidate complex cores with less assembly
• Integrate organic rigging and risers for less scrap
• Eliminate the lead time, cost, and storage of traditional tooling
SEE THE S-MAX® IN ACTION!
The S-Max® features a 1260-liter build box for rapid product development and reliable production of sand molds and cores. The fully automated printhead increases print speed, and advanced powder compaction offers leading green density and strength of complex designs. The S-Max can process all binder systems, including furan, phenolic, and inorganic, and is adjustable to produce cores and molds in a variety of foundry sands, from silica to ceramic.
Need a quote or estimate for your project, prototype or casting? We’re ready to help.
S-MAX® SPECS
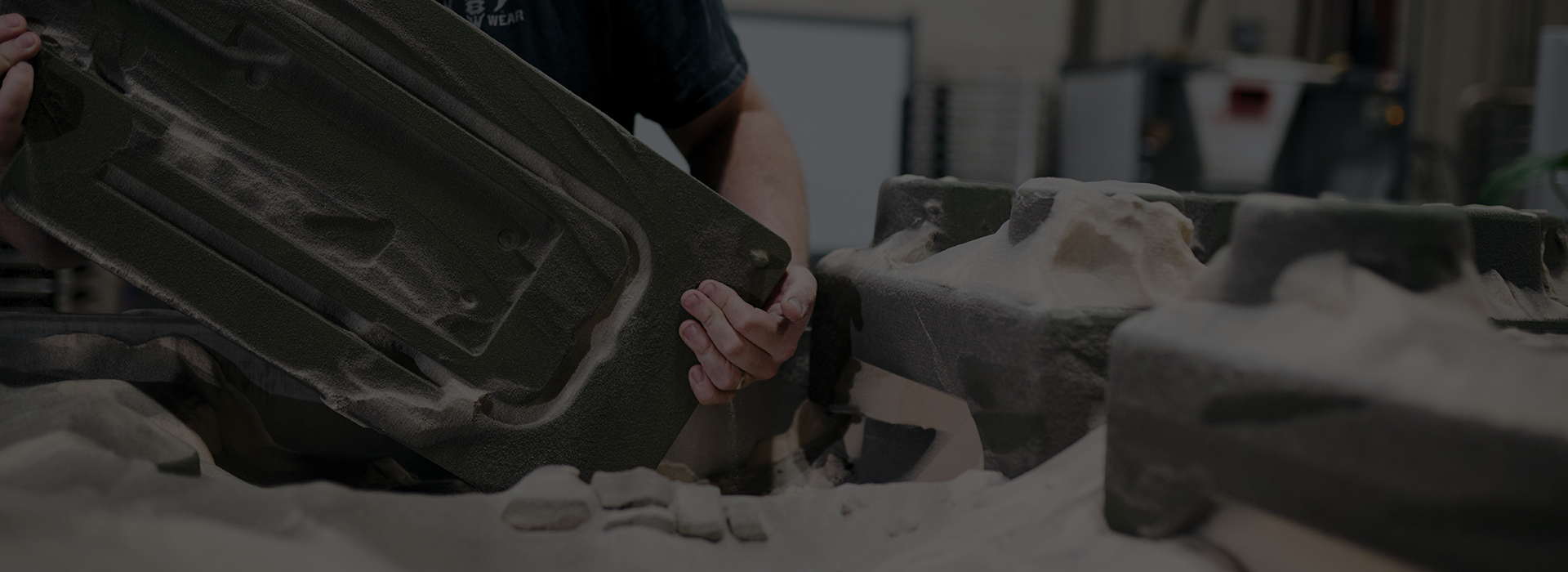
HOW CAN ALPHA HELP YOU
Get faster delivery, design freedom, and cost savings with 3D-printed molds and cores. Receive complex castings in days, not weeks—no patterns or extra labor required! Alpha can take you from prototype to production all under one roof!
WHAT EQUIPMENT DOES ALPHA USE FOR 3D PRINTING?
Alpha Foundry’s in-house ExOne S-Max 3D Sand Printer advances mold and core production with high-precision, speed, and design integrity. Our advanced technology exceeds in producing highly intricate designs, undercuts, and internal passages without the issues of traditional tooling constraints.
WHAT KIND OF CASTINGS ARE AVAILABLE?
Time and accuracy. The ExOne™ 3D sand printing process is super-efficient, with most projects taking no more than a few hours to complete. This alone opens the door to more prototype and small batch projects. We cast aluminum, grey and ductile iron, and ZA12 alloys in both 3D sand for small quantities as well as production volumes with our Alpha Process shell sand molding process. We can even produce hybrid castings using 3D printed cores for complex internal geometry with Alpha Process production molds.
What are the benefits of 3D printing for sand casting with Alpha Foundry?
3D Sand Printing allows for real casting production immediately, without the need to wait on tooling/pattern development. It also allows for complex geometry, fewer cores with less variation due to core assembly, and general casting designs that would be nearly impossible with hard tooling and real-world pattern limitations.
How does Alpha Foundry make 3D Sand Printing competitive for production?
We call cleaning 3D sand prints “depowdering.” Depowdering can become an unnecessarily time-consuming, labor intensive and costly manual activity that creates a bottleneck compared to the speed of the core printing process. The fastest, most efficient and careful way to clean 3D printed sandcastings is with ShotShower™. ShotShower™ can not only reduce labor costs but increases quality and lowers scrap rates…and frees up employees for productive work elsewhere in your operations. See hotideasllc.com to learn more.
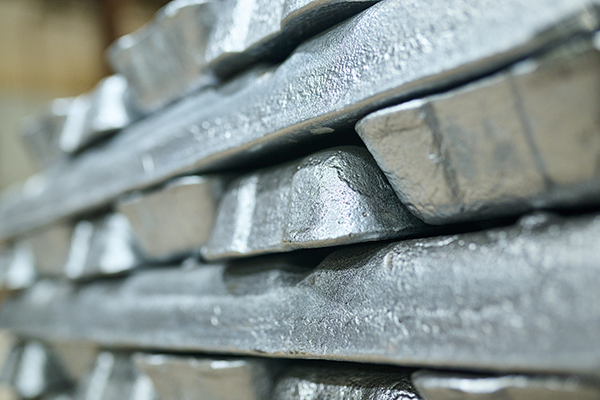
With the S-Max® we have increased capacity, enhanced production, and can offer our customers more value.
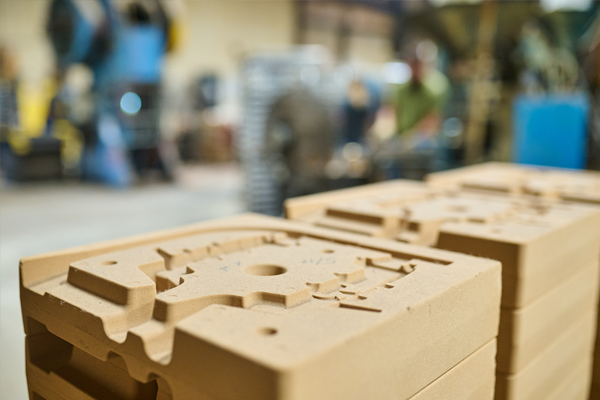
Faster, more efficient shell sand castings. Translation: premium castings without a premium price.