Changes for the Foundry Industry
It’s February, and we are beginning to see changes. Changes in the weather, and the midwestern ice and snow meltdown has begun. When it comes to winter weather here in Missouri, changes are always happening.
Besides the weather, changes are happening in our industry. The foundry business is seeing many new changes, especially in the way we produce our molds and cores. Technology has finally found its way into one of the oldest industries on our planet. Today, technology has given us 3D Sand Printing, and with this new technology, we now have a whole new way to create castings in sand produced molds.
What does 3D Sand Printing offer our industry? Enhanced Design Flexibility
One of the most notable benefits of 3D sand printing is the ability to produce highly complex and intricate designs that would be nearly impossible or too expensive to create using traditional methods. Unlike conventional sand casting, which relies on molds that need to be made from rigid materials, 3D sand printing allows for the creation of detailed geometries with minimal restrictions. This opens a wide range of design possibilities and enables manufacturers to create optimized components for specific functions, thereby reducing the need for multiple parts or complex assemblies. For industries such as aerospace and automotive, where lightweight, efficient, and highly durable components are crucial, this design flexibility is a game-changer.
How will this affect our customer that relies on our tried and proven methods? Will this style of 3D Sand Printing benefit them? Faster Prototyping and Production
The traditional prototyping process can take weeks or even months and involves the creation of molds, tooling, and other preparatory steps. 3D sand printing, on the other hand, significantly reduces this time. Once a digital model is created, the object can be printed in a matter of hours, allowing for rapid iteration and testing. This quick turnaround enables businesses to respond more swiftly to changes in design, reducing lead times for new products and making it easier to adapt to customer demands or market shifts. In industries like automotive and aerospace, where the speed to market can be a competitive advantage, this speed is invaluable.
What does 3D Sand Printing ultimately offer the foundry industry? Cost-Effective Production for Small Batches
For small-scale production runs, 3D sand printing can be significantly more cost-effective than traditional manufacturing methods. In conventional sand casting, the cost of creating molds, setting up machinery, and producing small quantities is often prohibitive. With 3D sand printing, there are no costly molds to create, and the technology can efficiently produce small batches of custom or specialized parts. This makes it particularly useful for industries that require custom or low-volume production, such as in the production of spare parts or prototype components.
How Alpha Foundry can introduce you to 3D Sand Printing-
Give us a try, send a file, let us show you how this amazing new technology can benefit your casting challenges. If you like it, great- let’s get to work. Contact us via email at info@alphafoundry.com or (636)745-9379, ask for Ryan Barron.
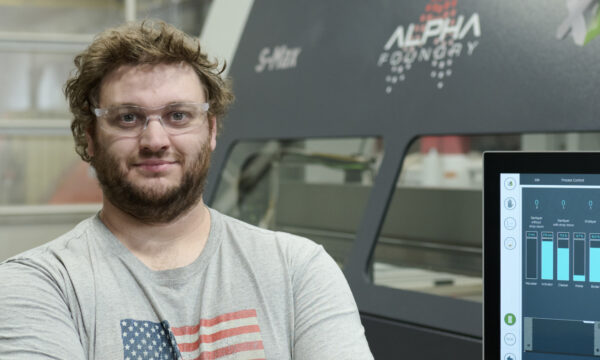
First Joe sets up the project in 3D printer
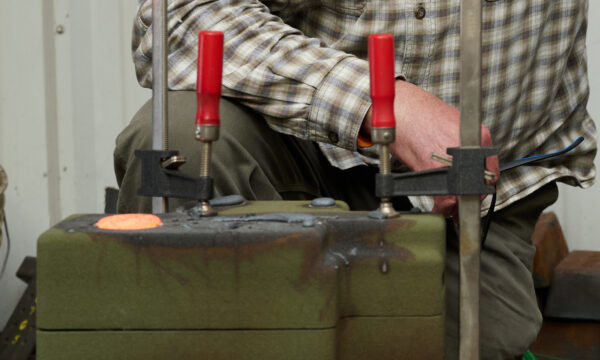
Next iron is poured into the mold and cools
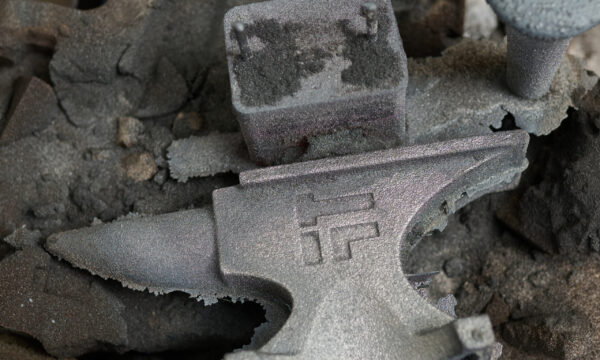
When cooled, the sand mold is separated
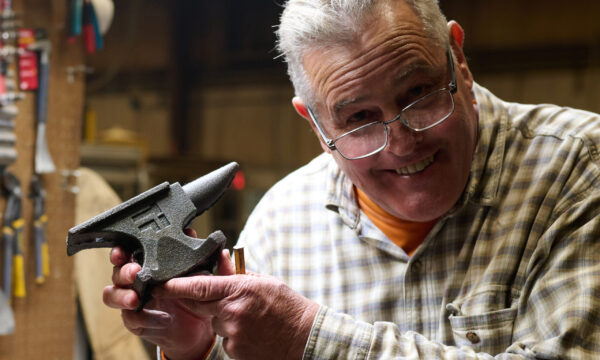
Ultimately, the molded product is finished